Miniature Tidal Generator
A new experimental apparatus has been developed, aiming to minimize size, weight, and complexity of the Tidal Generator concept, rendering the apparatus adaptable for centrifuge modelling. The key innovation of the developed “Miniaturised Tsunami Generator” – MTG (external page J98) is the ability to recirculate water around the model space. The water that inundates and then passes beyond the model space is recirculated back into the reservoir and reused, maintaining the water flow that is necessary to achieve the desired large wavelength. By recycling water that has inundated and then flowed out of the model space, we can drastically reduce the length of the channel, only producing a small portion of the target wave form at any time. This allows a drastic reduction of the dimensions of the apparatus and of the water reservoir that is required to produce the wave.
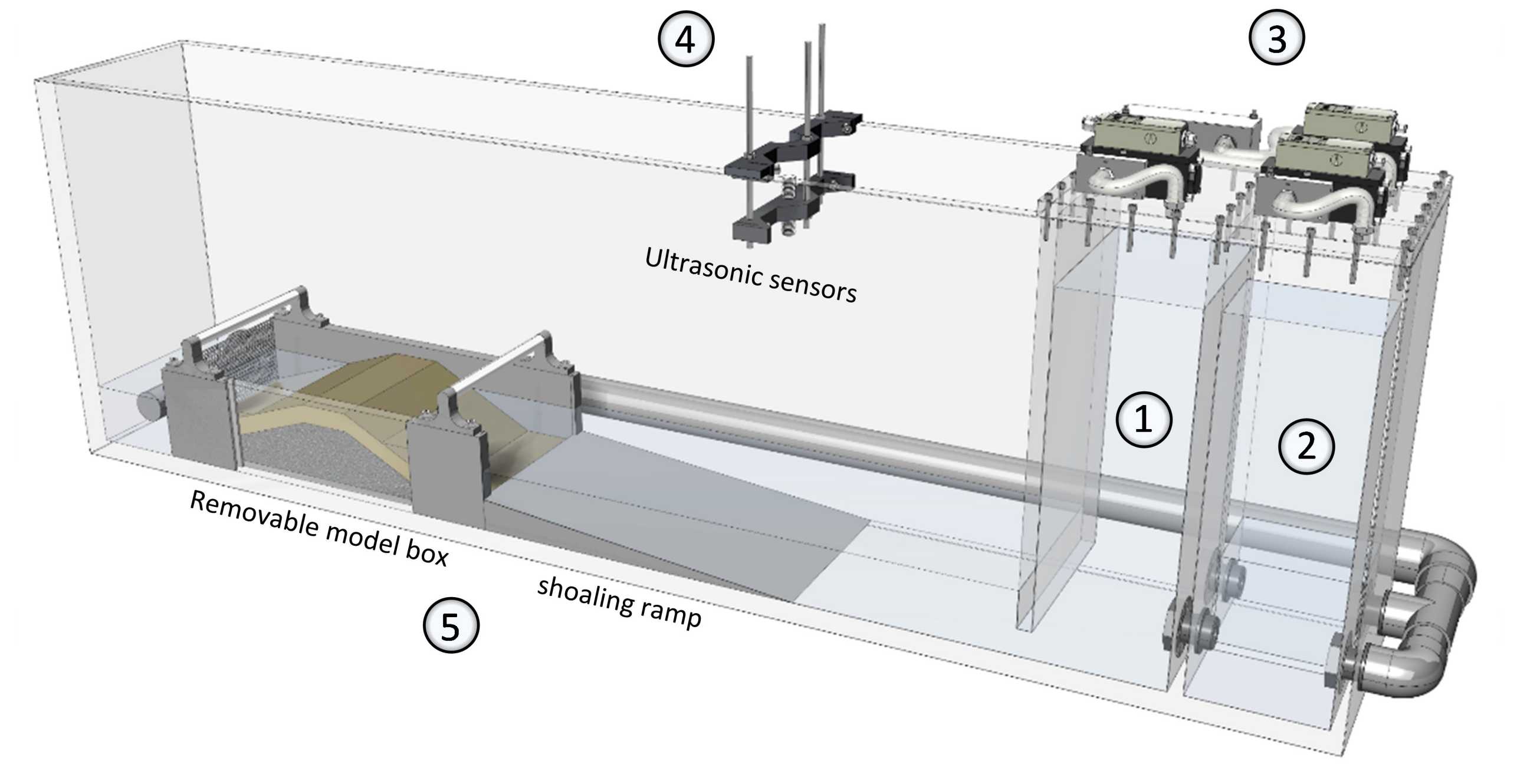
In order to keep the apparatus as mechanically simple as possible, the air pressure used to control the tidal tank is also used as the means for pumping. The addition of two extra smaller reservoirs, along with two sets of one-way valves, forms the “pump”, which operates like a pair of bellows. Water is drawn into each secondary reservoir from the far model boundary via application of vacuum, and then evacuated back into the tidal tank using atmospheric pressure. The one-way valves ensure that this process can only happen in one direction, so that water can only be drawn from the far model boundary behind the model space and only evacuated into the main reservoir. Two reservoirs allow semi-continuous flow, with one tank filling up, while the other is discharging.
To allow centrifuge adaptation, the MTG is designed to be as compact as possible, having a total length of 2m, a breadth of 0.3 m and a height of 0.5m. The flume is 1.8 m in length and the initial water depth at the model space is minimum 5 cm. At a 1:100 (N = 100) scale, this corresponds to a prototype of 180 m length and 5 m minimum depth. Geotechnical models are constructed outside the apparatus, in a model box of 0.5 m length and 0.2m height (50 m x 20 m at prototype scale), which is then installed into the flume. The removable model box allows pluviation using the same sand raining system used for centrifuge testing. The model box is equipped with porous end plates of variable height, which allow for water infiltration and transmission of pore pressures through the longitudinal boundaries. A Perspex window is installed along the sidewall of the model box to allow capturing digital images of the model to be subsequently used for calculation of soil displacements and deformations employing PIV.
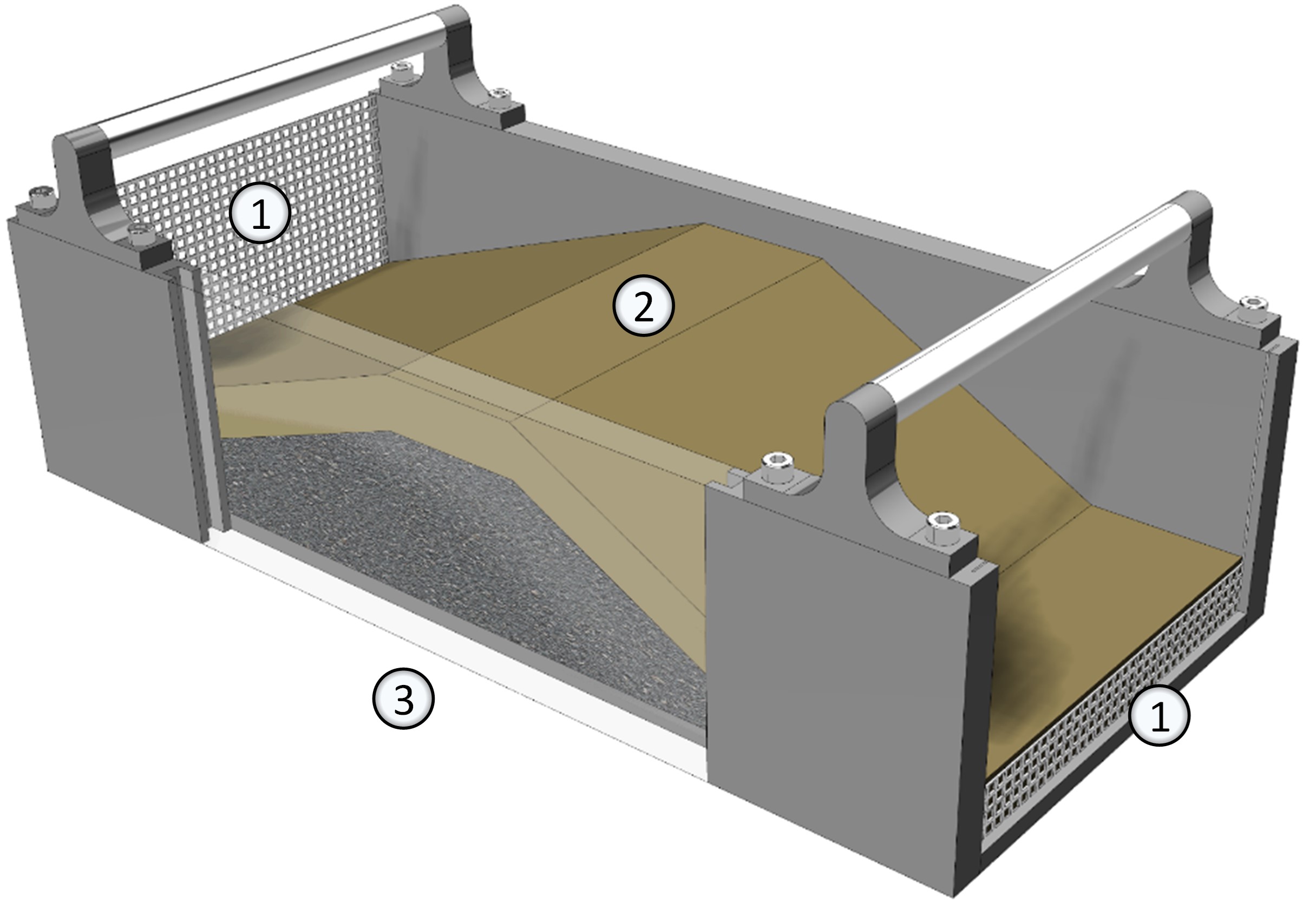
The MTG can be used to satisfactorily reproduce wave forms greater than 40 m in length (model scale), which is generally the range of interest for the study of Tsunamis (greater than 40 km at prototype scale). Currently, there are some limitations on the height of the wave that can be produced, which are related to the maximum discharge rate of the primary tank, which is a function of atmospheric pressure and the differential pressure over the opening of the tank to the flume. In the case of the centrifuge-mounted MTG (C–MTG), which is currently under development, this shortfall will be modified by the addition of a pressurised air feed to the tank, allowing for more rapid discharge and thus greater wave heights.
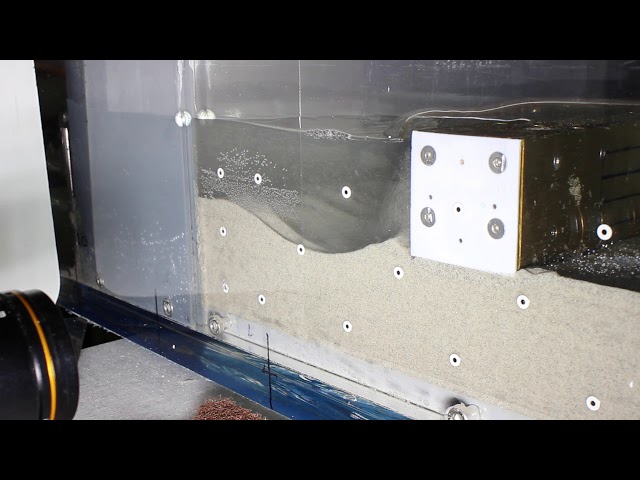

The MTG can only also be used to model scouring around bridge piers, which is one of the main causes of bridge failure. A novel hybrid approach has been developed to study the mechanical behaviour of a bridge foundation subjected to flood-induced scour (J**). A 2-step methodology is employed, decoupling the hydraulic (i.e., the scour process around the bridge pier) and the mechanical part of the problem. The first step simulates the hydraulic process in 1g using the MTG. The morphology of the scour hole is acquired through a 3D scanner, and the inverse of the scour hole surface is 3D printed to produce a mould of the scour hole. The 3D-printed mould is used to reproduce the scour hole in a centrifuge model, which is subsequently tested under Ng. The second step addresses the mechanical part of the problem, using 1:N scaled models tested at Ng, thus achieving correct scaling of the in-situ stresses.
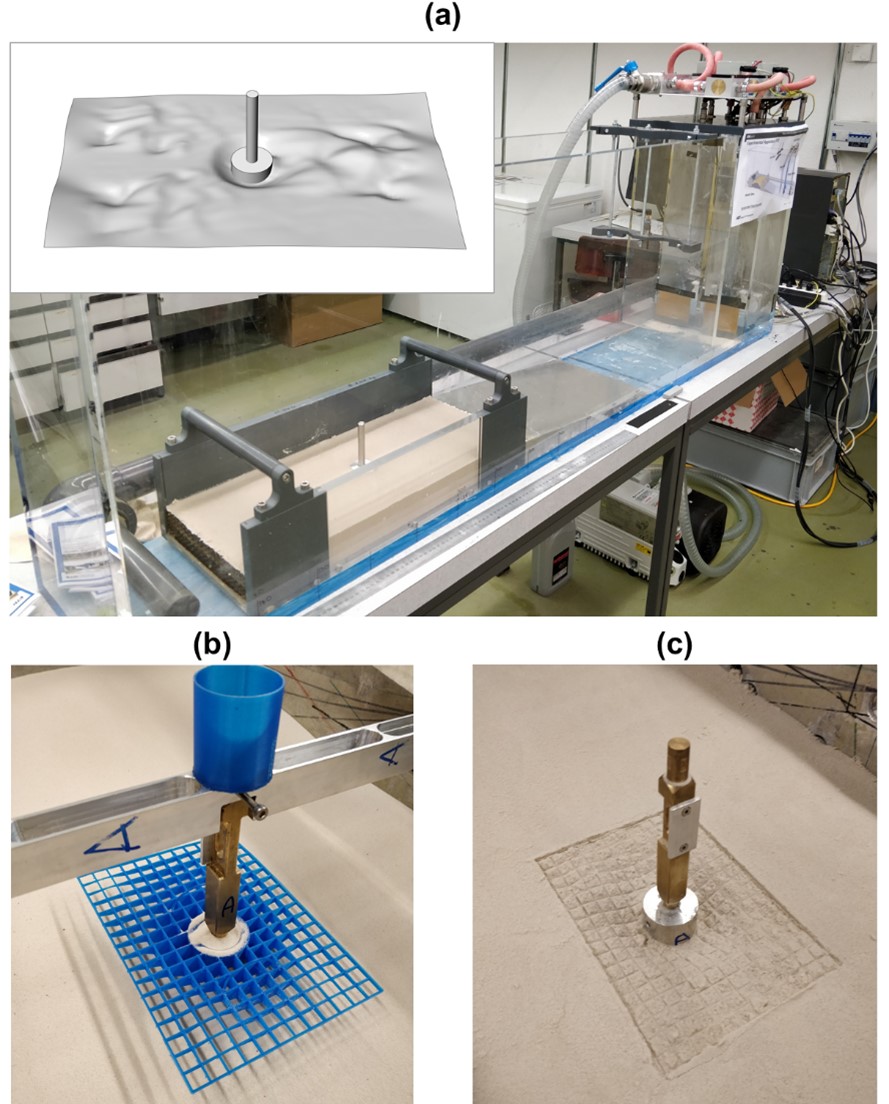
The direct (fully coupled) physical modelling of both the hydraulic and the mechanical part of the problem in a geotechnical centrifuge would be the best option to simulate the entire process as realistically as possible, providing that a proper scaling of the water flow characteristics is achieved. This will be possible with the centrifuge-mounted MTG (C–MTG), which is currently under development.