Geotechnical Centrifuge Center
Childpage navigation
Physical modelling is indispensable to derive insights on the key factors affecting the performance of geotechnical systems, to properly validate numerical models, and to evaluate the efficiency of innovative solutions (proof-of-concept). The Geotechnical Centrifuge Center (GCC) encompasses two geotechnical centrifuges, a 9 m diameter (500gton capacity) beam centrifuge and a 2.2 m diameter (440gton capacity) drum centrifuge, a cutting-edge earthquake simulator, a Miniaturized Tidal Generator (MTG), and a variety of actuators, tool platforms, and highly specialized devices and sensors. Our experimental infrastructure is predominantly used for research and teaching purposes. On demand, we also offer highly-specialized consulting services to the industry.
The properties of soil are well known to be dependent on the effective confining stresses, owing to its self-weight. When modeling a geotechnical system at a scale of 1:N, the confining stresses are N times smaller than the prototype. In order to achieve correct stress levels in the physical model, the geotechnical centrifuge artificially increases the self-weight of the physical model by applying an increased “gravitational” acceleration. In this way, a 1:N scale model tested at N times the gravitational acceleration (Ng) in a centrifuge will have the same effective stresses as the full-scale prototype, properly maintaining scale similarity and avoiding scale effects.
Under such enhanced gravity conditions, the time is scaled down by N2 for diffusion problems and N for dynamic events. This leads to an additional major advantage in terms of simulating long-duration processes in a very short time. For example, consolidation settlements, which may take 1 year in nature, can be simulated in less than 1 hour in the centrifuge by accelerating the model at 100g (the time is scaled by N2 for consolidation problems). In this way, the centrifuge offers the possibility to perform physical model tests of geotechnical systems in a much faster and more economical way than full-scale or field tests. In particular, for the seismic response of soil-foundation-structure systems, centrifuge modelling may be the only realistic solution, since large scale shaking table testing is prohibitive in terms of cost.
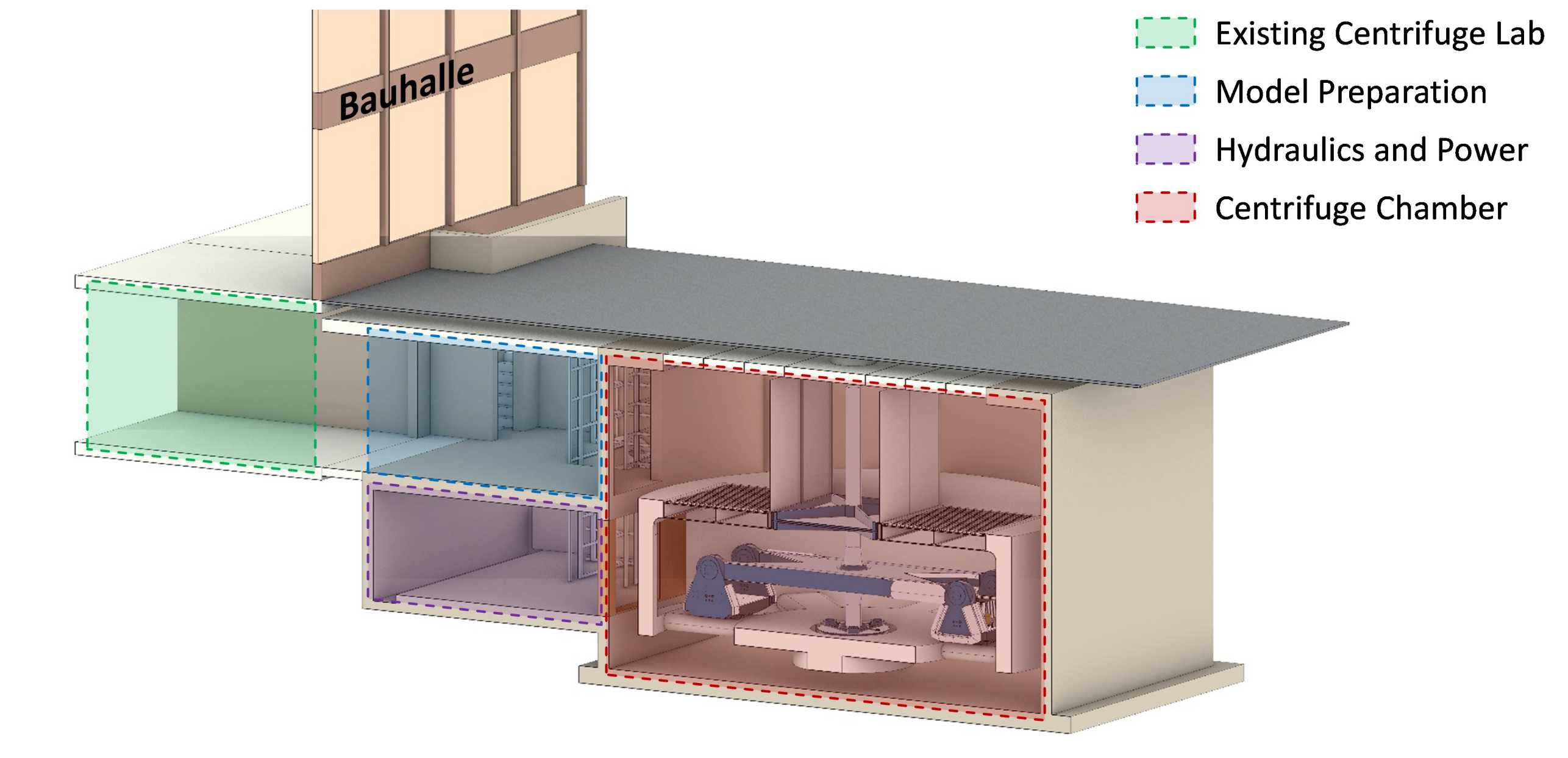
Due to the proximity of the new centrifuge facility to the future HPQ building (D-PHYS), which will include extremely sensitive to vibrations laboratories, a special design is employed where the centrifuge chamber is vibration isolated. The centrifuge chamber is decoupled from the external structure, sitting on specially-designed isolation springs. The springs are tuned to increase the period of the system, leading to significant attenuation of any centrifuge-induced vibrations. The vibration isolation concept was developed and analysed in-house, showing excellent performance. The 245 ton centrifuge chamber was successfully installed on the vibration isolation springs on August 14, 2020
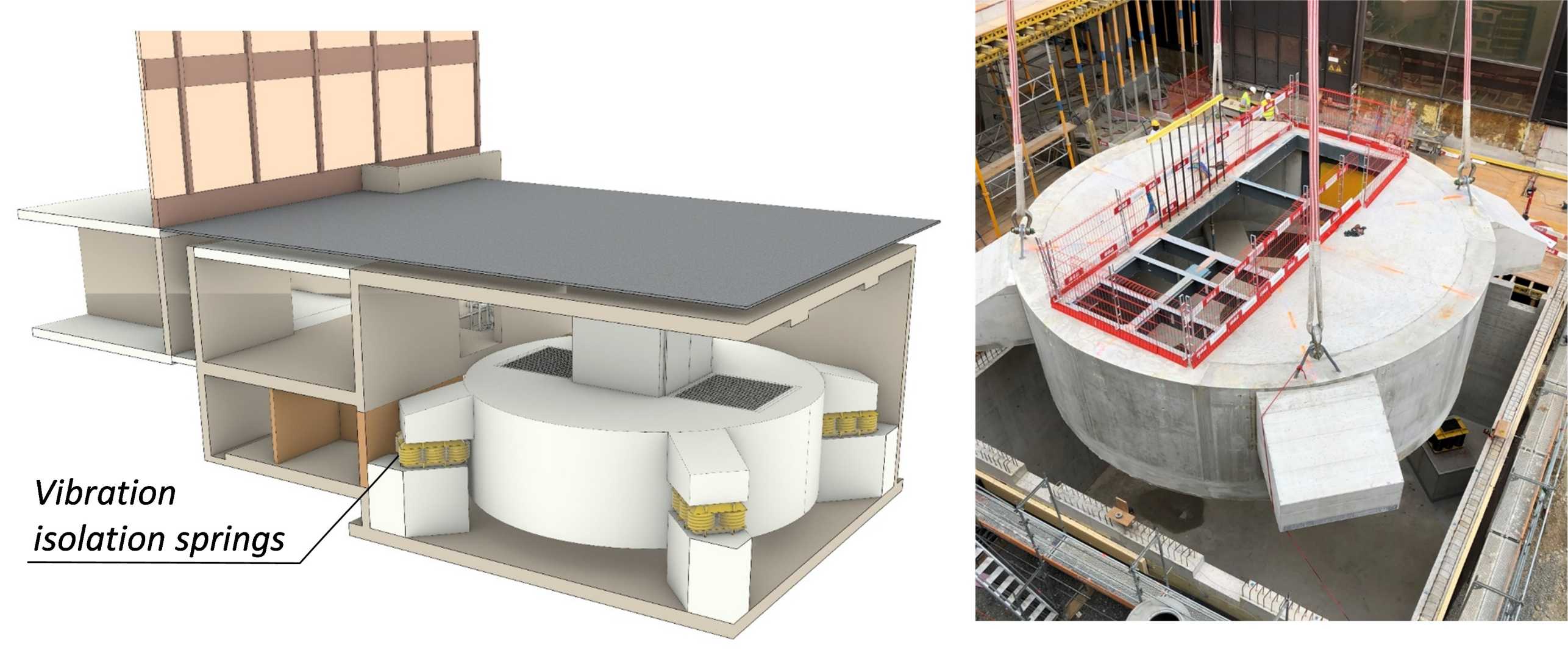
Beam Centrifuge
The newly-constructed beam centrifuge facility is connected to the pre-existing drum centrifuge facility on its upper floor, with the beam centrifuge installed on the lower floor. Besides the centrifuge chamber, the lower floor houses the hydraulic pumps (necessary for the supply of oil pressure to the hydro motors of the centrifuge and for the seismic shaker), as well as power and control units. The upper floor encompasses the model preparation laboratory, the housing of the upper axis with the corresponding slip-rings, and storage space. The control room is integrated in the pre-existing drum centrifuge facility, following the security guidelines of Cambridge University (Schofield, 1980) to ensure safe operation.
Click on the images below to explore each subcategory.
Drum Centrifuge
Established by Prof. Sarah Springman in 1999, the geotechnical drum centrifuge facility consists of a preparation laboratory, the centrifuge pit, and a control room, from which the technician, the project engineer and the proof engineer supervise the progress of the test (external page Springman et al. 2001). These three roles are based on the security guidelines at Cambridge University (Schofield, 1980) to ensure safe operation of the facility.
The drum centrifuge consists of a main channel (1), in which the model is built or placed, and a tool platform (2), where actuators and sensors can be mounted together with the data acquisition systems. With a diameter of 2.2 m, 0.7 m height and 0.3 m depth, the channel can be accelerated up to 440g carrying a payload of up to 2 tons. A key advantage of the drum centrifuge is that the entire channel can be filled with soil, creating a model deposit of 5 m length, which corresponds to a prototype of 2 km length, over 100 m depth and 300 m width. Smaller models can be tested using strongboxes, prepared outside and placed on the channel.
The rotation of the channel and the tool platform is provided by an external (4) and an internal (5) shaft, respectively. The tool platform can spin together with the channel, or independently. This allows stopping the tool platform during a test, allowing changes or adjustments of actuators and sensors mounted on the platform without stopping the test. In such a case, a shield is lowered to protect the stationary platform from the spinning channel. Communication between the on-board computer and the control room is provided by sets of electrical slip rings (6, 10, and 13). An additional slip ring is mounted on the tool platform over the internal shaft (5), allowing supply of water to the spinning model from an external source.
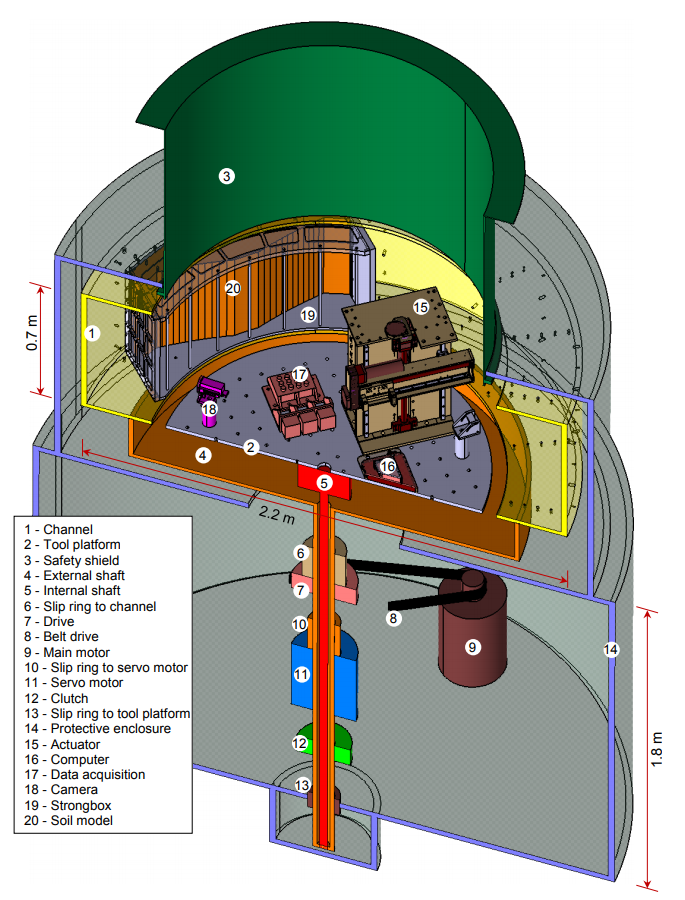
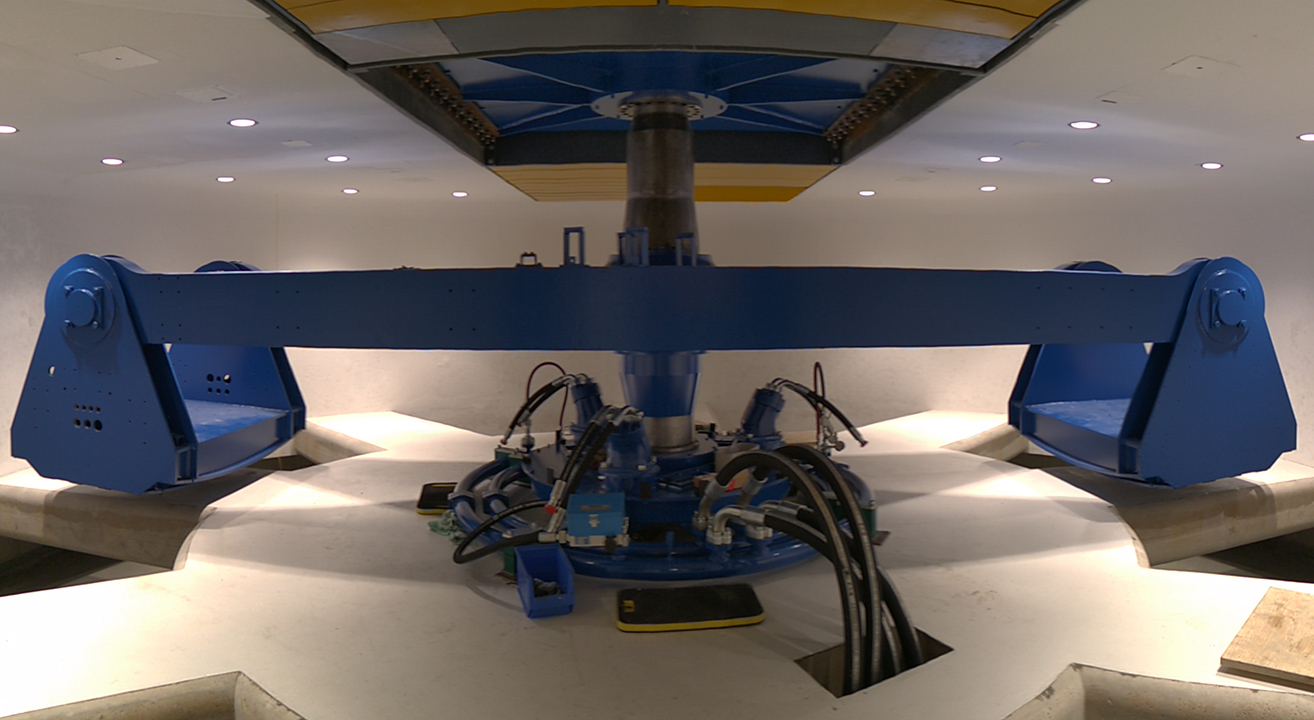
Besides the data acquisition system and the on-board computer, the tool platform is equipped with vertical and horizontal servo-electric actuators. In combination with the ability of the platform to rotate independently from the drum channel, the system allows actuation in 3 degrees of freedom (vertical, horizontal, and lateral). The actuators are equipped with load cells and laser displacement transducers to control and measure the results of the test. Depending on the specific needs of the test, different tool platforms are available, containing other types of actuators and instruments.
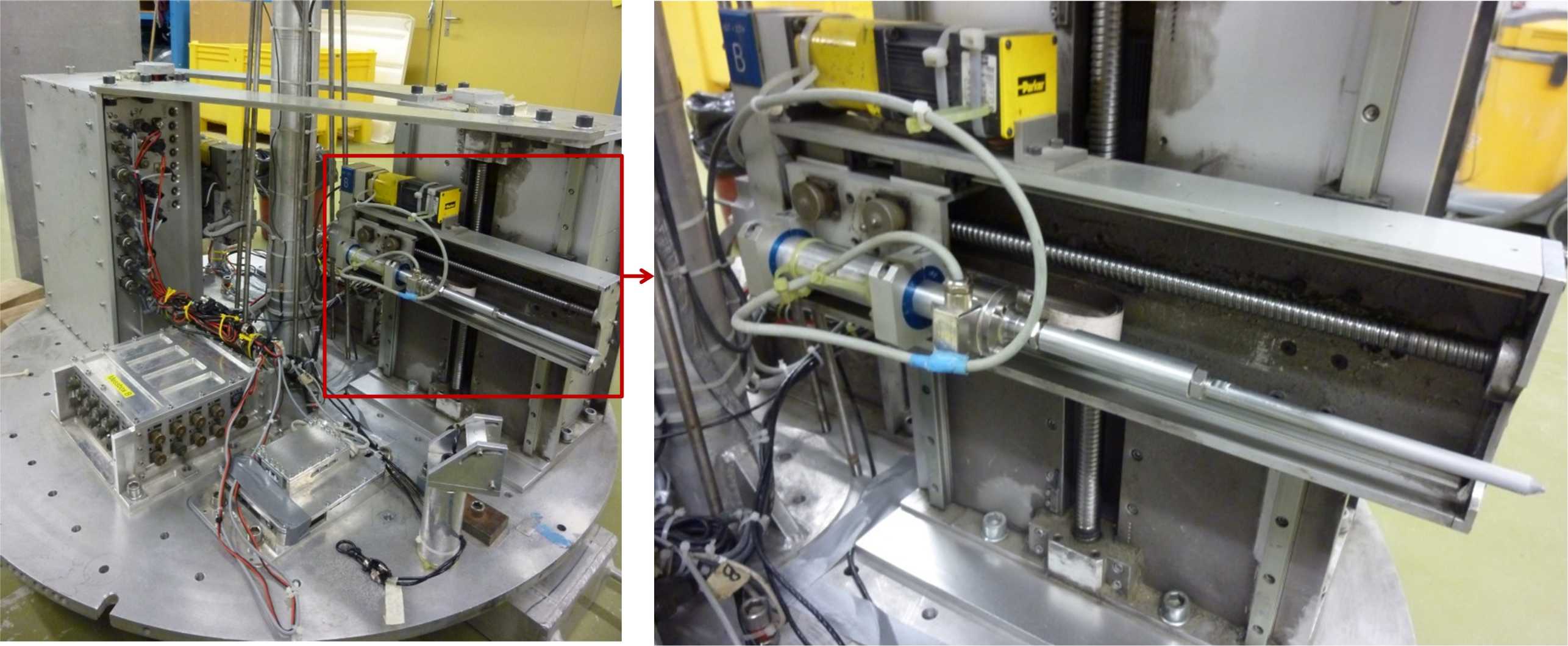
Click on the images below to explore each subcategory
Sensors
The Geotechnical Centrifuge Centre is equipped with a multitude of sensors, including high speed and high resolution cameras, accelerometers, displacement sensors, pore-pressure transducers, time-domain reflectometers, load cells, strain-gauges, and tactile pressure sensors.
Click on the images below to explore each subcategory