Triaxial
Four in-house developed triaxial testing apparatuses are available. Initially developed to conduct creep tests on snow samples (external page von Moos & Bartelt, 1998), the apparatus allows both strain-controlled and stress path tests. While for snow samples air was used as cell pressure medium, the current soil mechanics adapted design operates with water. Placed in a cold chamber, three such apparatuses were used for permafrost research (Arenson 2003). With a sample diameter of 56.4 mm and also equipped with bender elements, a fourth one was used to study lacustrine clays (Trausch Giudici 2004).
In the current configuration, 3 different axial load cells are available (2, 5 and 20 kN), allowing testing of different soil materials with variable sample diameters (50, 56.4, and 75 mm). A maximum cell pressure of 1000 kPa can be applied, while testing at low temperatures (down to -10°C) is possible, using the cold chamber. The devices are equipped with Bender elements, allowing the measurement of shear wave velocity, radial deformation with a custom-designed laser system, and also acoustic sensors. A recent development has introduced separate top and bottom control of pore water pressure, which can be used for permeability measurements, saturation of coarse grained material, and even inducing a hydraulic gradient during shearing.
The technical specifications of the triaxial test apparatuses are summarized as follows:
- Specimen diameter: 50, 56.4, and 75 mm
- Maximum cell pressure: 1000 kPa
- Changeable load cells: 2, 5 and 20 kN
- Temperature controlled cell liquid: down to -10°C (combined with the cold chamber)
- Bender elements for determination of shear wave velocity
- Local vertical strain and radial deformation measurement with laser system
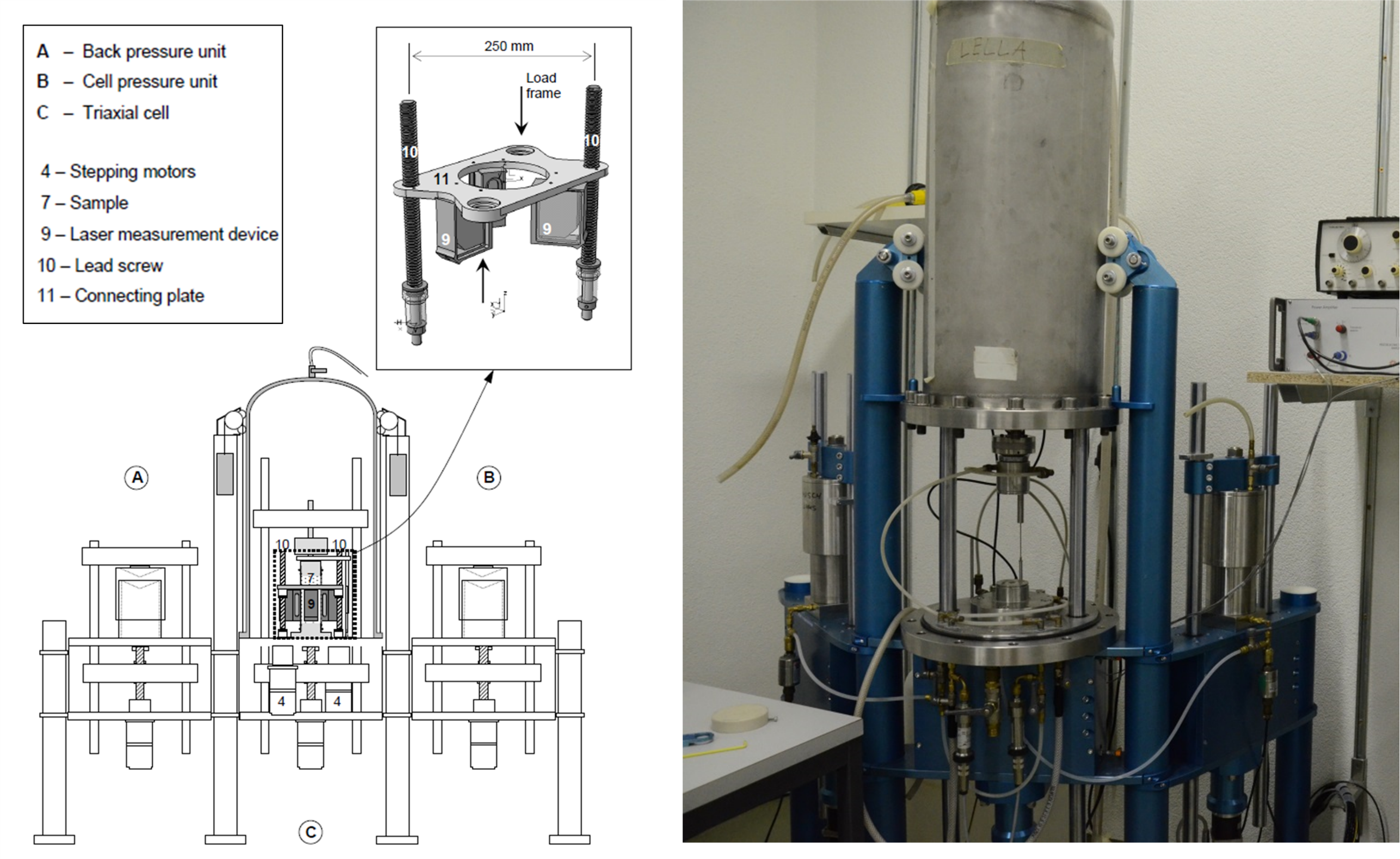